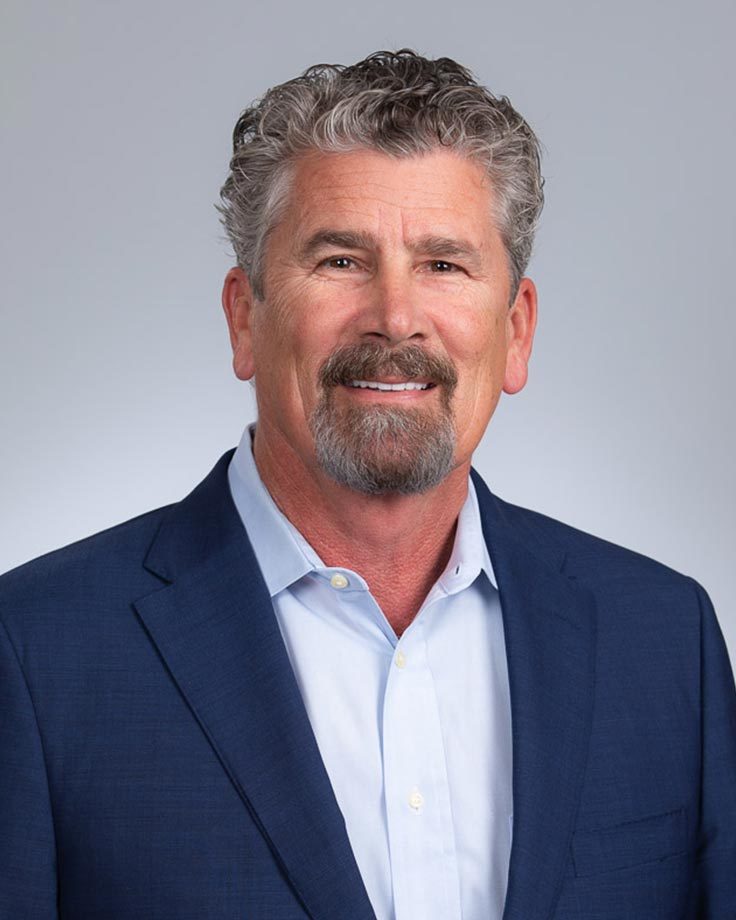
"I am pleased to present H&P’s 2024 Sustainability Report, marking another year of progress and commitment to sustainability and corporate stewardship. Our path towards sustainability is driven by our core values, what we proudly call “The H&P Way,” and our dedication to creating long-term value for our stakeholders."
- John Lindsay, president and chief executive officer, H&P, 2024 Sustainability Report
H&P has long recognized the importance of promoting sustainability across the organization and the broader oil and gas value chain. Our annual Sustainability Report updates and builds upon the information we provided in the previous year.
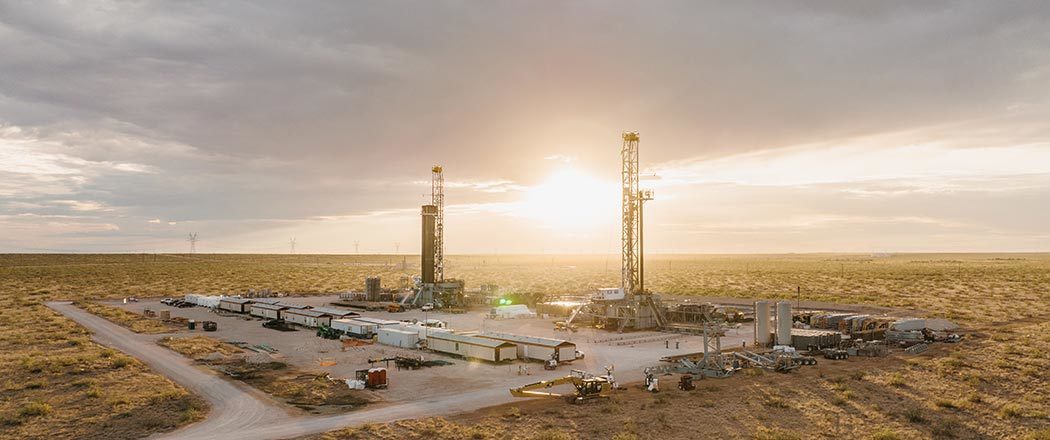
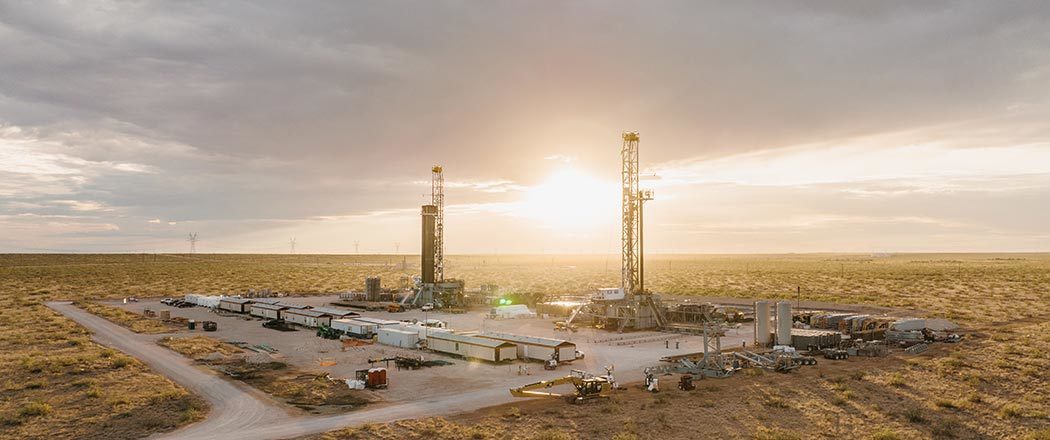
Additional Documents
-
Aligned reporting with leading third-party frameworks including TCFD, SASB and GRI
-
Engaged with Ernst & Young to provide limited assurance on select sustainability metrics
-
Achieved a 10.7% normalized greenhouse gas emissions (GHG) reduction in fiscal 2024
-
An average of 21 rigs ran on highline power, displacing estimated 7.8 million gallons of diesel fuel equivalent to 80,000 metric tons of CO2e
Corporate governance at H&P encompasses the oversight mechanisms that help us mitigate risk and facilitate the execution of environmental, social, and governance initiatives. Learn more about our policies and meet the Board of Directors through the links below.
Governance and Policies Meet Our DirectorsContact the Sustainability Team
Questions or feedback regarding H&P's sustainability efforts? Please contact us.