Operator Saves 12 hours+ of trip time, equating to $35,000 USD
Challenge
A Well Site Leader working on a rig in West Texas’ Delaware Basin identified that their conventional mud motor was stalling at a much lower differential pressure than the motor was supposed to be rated for, indicating that the motor in hole was weak. Making an unplanned trip to replace the motor could cost approximately $50,000, on top of the costs of the day rate if they had to pull-out-of-hole (POOH). More importantly, an extra trip would mean increased exposure to safety incidents as there is an increased likelihood of a serious injury or fatality (SIF) event every time there is an unplanned trip.
The operator and the H&P team knew they needed to find a solution that would allow them to reach total depth (TD) without needing an extra trip.
Solution
H&P recommended the newly released StallAssist® software which is designed to detect, mitigate, and recover from downhole stalls. As pressure is reaching the stall rating, the system continually and simultaneously evaluates several factors, including: pressure, the speed in which the pressure is rising, and motor specifications. These dynamic, real-time calculations help lessen the severity of pressure that is outside motor limitations.
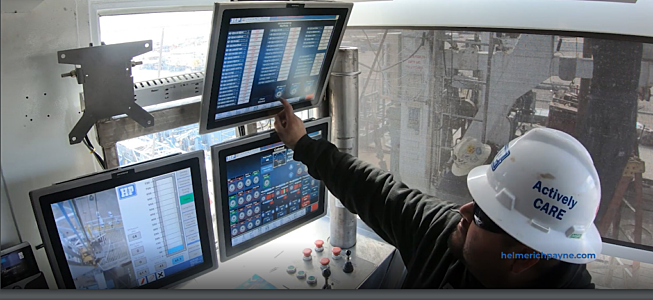
In this case, where the team suspected a weak motor, H&P lowered the StallAssist software setpoints to try and detect a stall sooner and prevent the motor from reaching the maximum stall PSI rating, helping to extend the life of the weak motor.
While getting the motor to TD was the immediate challenge, drilling operations need a myriad of technologies to help ensure an optimal outcome. This operator fused a series of directional drilling automation technologies like the Bit Guidance System and AutoSlide® technology with failure prevention solutions like StallAssist and FlexB2D® 2.0 software to help achieve consistent, repeatable results with less failures.
Outcome
The operator continued to drill and though the motor was weak, it was able to reach TD without experiencing an unplanned trip or, other worst-case scenarios like tools lost in hole or a sidetrack. By avoiding the extra trip, this operator saved at least 12 hours of trip time, equating to $35,000 USD.
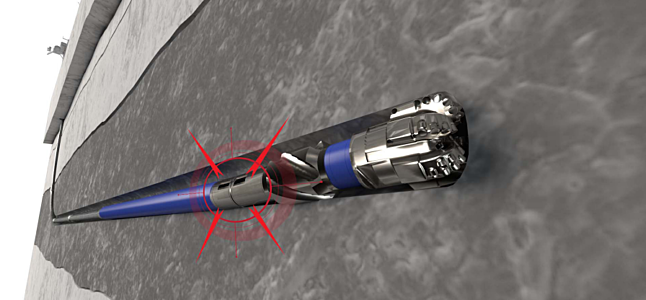
Past performance is not a guarantee of future results. Any statements regarding past performance are not guarantees of future performance and actual results may differ materially. © 06/2022 HPCS019